工业的等静压烧结和干压烧结是两种不同的成型与烧结工艺,主要区别体现在成型方式、设备要求、产品性能和应用场景等方面。以下是两者的详细对比:
1. 成型原理与压力方式
等静压烧结(Isostatic Pressing)
成型原理:通过液体或气体介质(如油、水或惰性气体)向弹性模具(如橡胶或塑料)内的陶瓷粉末施加各向同性的均匀压力(通常为100-300 MPa),使粉末颗粒在三维方向上均匀密实。
压力特点:各向同性压力,无方向依赖性,可消除密度梯度。
模具要求:使用柔性模具(弹性体),模具成本较低,但需要高压容器。
干压烧结(Dry Pressing/Uniaxial Pressing)
成型原理:将陶瓷粉末填充到刚性金属模具中,通过机械冲头单向或双向施加压力(通常为50-200 MPa),使粉末在单一方向或两个垂直方向上压缩成型。
压力特点:单向或双向压力,易导致密度分布不均(如边缘密度高、中心密度低)。
模具要求:高精度刚性模具(如或钢),模具成本较高,但无需高压容器。
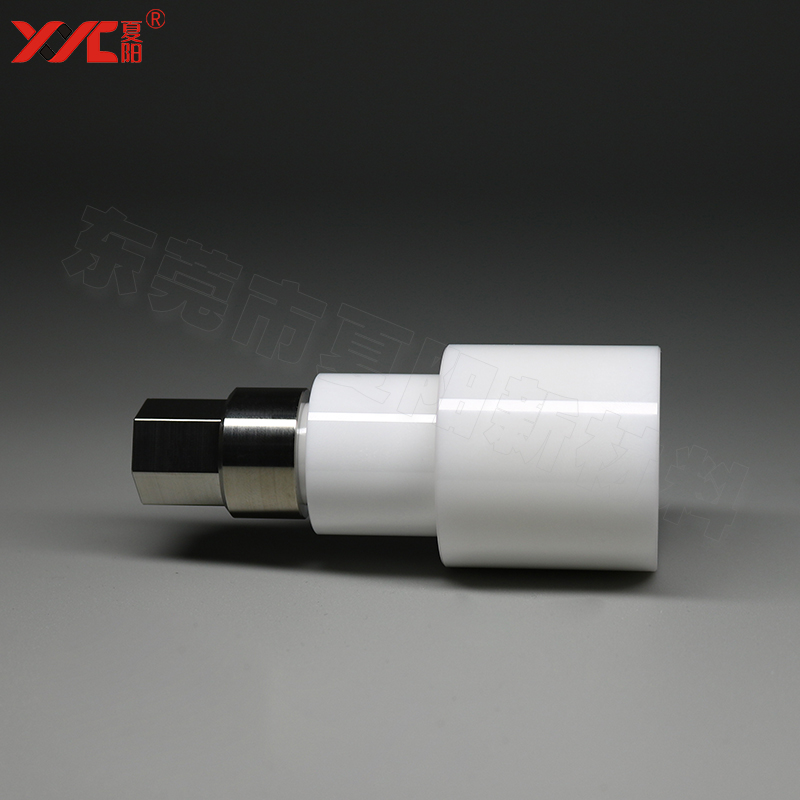
2. 产品特性对比
特性 | 等静压烧结 | 干压烧结 |
密度均匀性 | 极高(各向同性压力消除密度梯度) | 较低(存在密度梯度,尤其是复杂形状) |
形状复杂度 | 适合复杂形状(如异形件、空心件) | 适合简单形状(如平板、圆柱体) |
尺寸精度 | 较低(弹性模具变形影响) | 较高(刚性模具保证尺寸精度) |
孔隙率 | 低(高压下颗粒结合紧密) | 较高(局部区域可能残留孔隙) |
力学性能 | 强度高、各向同性性能好 | 可能存在各向异性(沿加压方向更强) |
3. 设备与成本
等静压烧结:
设备成本:高(需高压容器和介质循环系统)。
生产效率:较低(装模、加压和脱模周期长)。
适用场景:小批量、高附加值产品(如航空航天、医疗陶瓷)。
干压烧结:
设备成本:较低(传统机械压机即可实现)。
生产效率:高(适合自动化连续生产)。
适用场景:大批量、简单形状产品(如电子基板、耐火砖)。
4. 典型应用领域
等静压烧结:
高性能(如氮化硅轴承、氧化锆人工关节)
精密电子陶瓷(如多层电容器、压电陶瓷)
特殊形状部件(如涡轮叶片、复杂模具)
干压烧结:
普通工业陶瓷(如绝缘子、耐火砖)
电子元件基板(如氧化铝基板)
日用陶瓷(如陶瓷刀具、耐磨衬板)
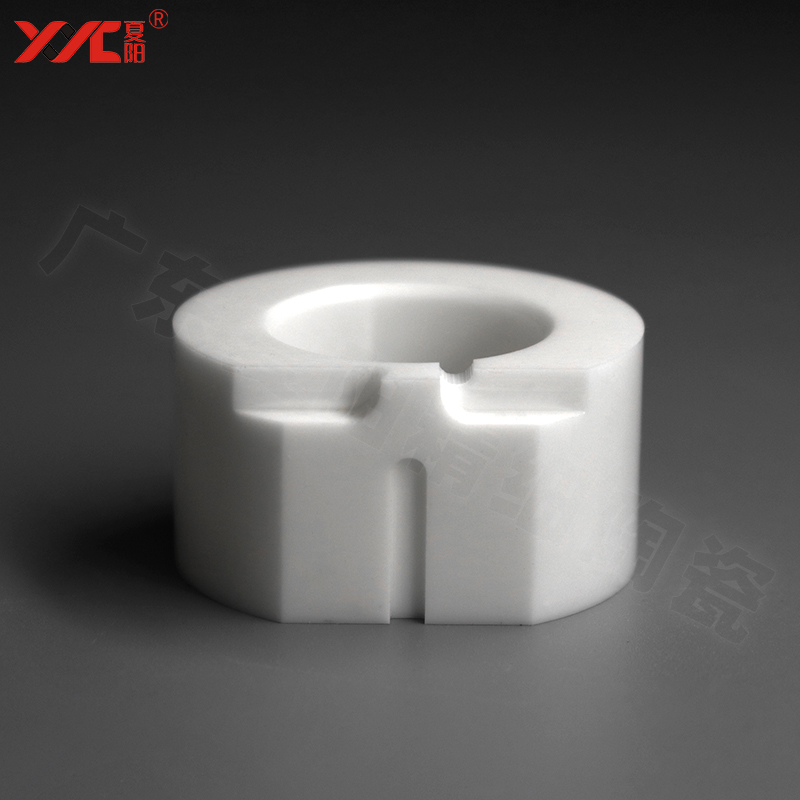
5. 工艺局限性
等静压烧结:
难以实现高尺寸精度(需后续加工)
对粉末流动性要求较高
干压烧结:
无法成型复杂或薄壁零件
密度不均匀可能导致烧结变形或开裂
总结
等静压烧结适合对均匀性、复杂形状和高性能要求严格的场景,但成本较高;干压烧结则更经济高效,适合大批量简单零件的生产。选择工艺时需综合考虑产品需求、成本预算和生产规模。
东莞夏阳新材料有限公司研发制造的先进精细陶瓷是近年兴起的新型材料,具有耐超高温度、高硬度、耐酸碱腐蚀,不导磁、不导电,特殊光色效果,在航天航空、通信、汽车、化工、医疗、电子、精密机械等军工民用行业有广泛的用途。正成为未来最具前途的新材料之一;夏阳拥有多名材料博士和陶瓷工程师;设备齐全的实验室;全套先进的制造检测设备:气压烧结炉,真空烧结炉,冷等静压,干式压力机,注塑成型机、炼泥设备等;拥有成熟的干压成形、冷等静压成形!制造生产有氧化锆、氧化镁锆、增韧氧化锆、氧化铝、氮化硅、碳化硅和彩色陶瓷。如需咨询更多材料以及解决技术难题可以直接联系我们:185 8811 0628